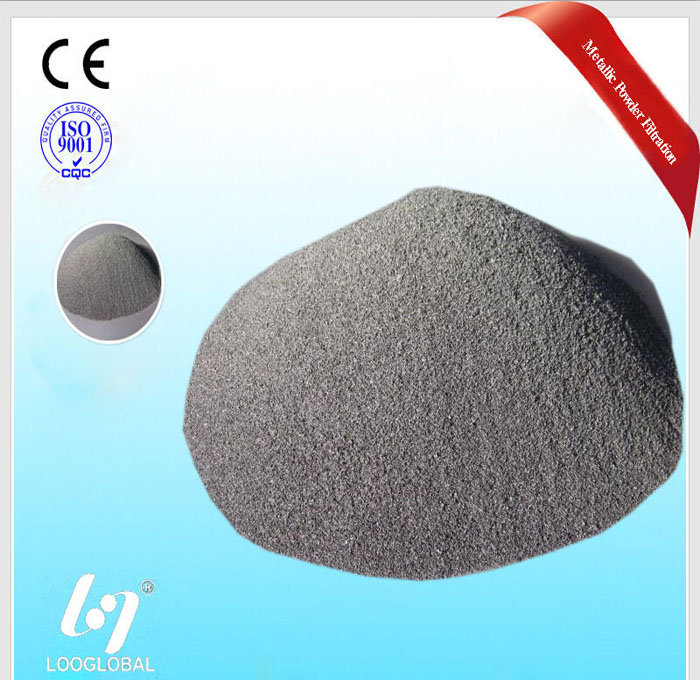
316 Metallic Sieve Powder
-
Min Order
1
-
Product Unit
Pieces
-
Origin
China Mainland
-
Payment
- Contact Now Start Order
- Favorites Share
- Description
Product Detail
Why S.S Metal Sand is the best choice for fiber spinning
1 ) Extension Component life, greatly reducing the production cost.
Metal sand filter material will be more than 3 times long life than the
glass beads,common sand and other filter materials.Because of its high
profiled metal sand, large surface area, strong ability filter
impurities to extending the life of components. Reduces the component
related accessories(filters, washers, etc.)cleaning cost.
2) To Reduce the spinning yarns breakage, irregular convex metal sand
sharp features are unmatched by conventional filtration material, this
sharp with high hardness which are not easily deformed even under
pressure of 40MPA.During the filtering,can pierce the bubbles,barriers
and aggregated particles to improve filtering precision.
3) Stable component pressure,slow and steady in the pressure rising,to
avoid instability caused by pressure fluctuations in
production,instability quality and etc.The metal sands ability will not
change by the changes of pressure and temperature.
4) Improve the uniformity and the melt spinnability, stainless steel is a
good conductor of heat which can guarantee melt sands temperature to
fit the component compartment temperature.
5) Stability chemical ability.No adverse reactions with polyester melt.
6) Easy to use, no need cleaning& drying like glass beads, sand,
emery.Because our production has been conducted in high-pressure
cleaning process, the factory’s products have done in clean.
Cost Savings
If 25 days cycle life of sea sand ( usually 25-30 days ) , metal sand 40
days ( usually 45-60 days ) , fiber fineness 100D, a component assembly
with an estimate of the amount of sand 200g . That is eight times using
sand replacement components ( 25 days * 8 = 200 days ) , and the use of
metal sand replacement five sub-assemblies ( 40 days * 5 = 200 days )
to the same production cycle time.
A component cost by using sea sand as follows: a mat 5$, cleaning costs
1$( water, electricity, gas , materials, labor, management, etc., many
enterprises greater than 1$) , the component materials under the machine
loss of 100 grams ( Total 0.2$ ) , the open position marker 200 grams (
count 0.4$ ) , you need to sand the cost is 0.1$, the total cost of a
cycle : ( 5 +1 +1 +0.2 +0.4 ) * 8 = 60.8$; If under the same conditions ,
a component requires metal sand costs about 1.2$, the use of metal sand
a cycle costs as: (5 +1+1 +0.2 +1.2 ) * 5 = 42$, a savings component a
cycle cost 60.8-42 = 18.8$. Because the metal sand brought improvement
of product quality , as well as the stability of the production process
to improve the benefits and costs of production, on the use of metal
sand the direct impact of cost savings is about 20.1% than other
materials, the metal sand a year for one cost-saving will be 24$.
Specific to different companies will vary ,some companies cyclicality
can reach 90 days and will be more cost savings.
Excellent performance of metal Sand in production
1.Excellent metal sand structure.
2.The cycle of metal sand generally will be more than 40 days, the longest period can be 90 days.
3.Excellent stability for FDY, porous fine denier , cationic, PBT, PTT,
nylon , and other differentiated functional fibers spinning.Such as the
75D/144F POY and etc.
Metal sand technical parameters
1, Metal content
Element C Cr Ni Mo Si Mn Fe
Acceptable range% 0.1-0.2 17-22 4-13 1-3 1.5-3 0.4-0.7 Basic
Note: Can be adjusted according to customer requirements.
2.Density (unit: g / cc)
Micron Mesh Density(G/cm³)
1651~833 10~20 1.2~1.5
833~350 20~40 1.6~2.0
350~245 40~60 1.65~2.3
245~198 60~80 1.7~2.6
198~165 80~100 1.8~3.2
Note:
A.Density Test Methods:Put 800 cm3 empty beaker on the platform, then
fall into metal sand at a distance of 20 cm,stopped when the beaker
filled the sand.Weight in grams and the volume of the beaker will be the
metal density.
B. Above density only as a reference, the actual use of the density will
be according to the specifications and requirements of the pressure
component set.
Component Pressure
Should be ± 10bar after 6 hours the machine components working.
The appearance checking
Uniform size,no rusting,uniform acute angle, spherical objects = 0.5%.
How to use
1 The metal sand in the our production process has been rigorous
cleaning and filtering , no need washing or filtering before using.
2. Before using , please check the specification.
3. Avoid dust and debris into the metal sand bag.
4. Several specifications layering can be used, in several
specifications between each layer is best to put a stainless steel mesh
filter.The closest spinneret will be higher mesh sand.
5. According to the requirements of the production process of the metal
component ,you should use a copper bar to hit to increase its density ,
and then use a stainless steel rod ( rod length 15 centimeters,end must
be smooth ) to press on the position of the metal sand surface(About 10
kg pressure,clockwise or counterclockwise rotation around the metal sand
surface) to void the same positions uneven density.
6. No gap allowed.
7. If boost slow or for a long time does not boost, this is a normal phenomenon.
8.When reach maximum pressure Please timely replace the components in order to avoid producing substandard products.
9.This product is disposable after use which can not be used again.
10.Our metal sand is long life ,please track or record the
time.Meanwhile,Please make the silicon nozzle plate trimmed regularly to
ensure the quality and continuity.
- Non-metallic Package Hydraulic Presses 1 Pieces / (Min. Order)
- 304 Metallic Filtration Powder 1 Pieces / (Min. Order)
- 316 Metallic Sieve Powder 1 Pieces / (Min. Order)
- Mono-(6-ethanediamine-6-deoxy)-beta-cyclodextrin 1 Pieces / (Min. Order)
- Amphetamine (AMP) Urine Drug Test Kit 1 Pieces / (Min. Order)
- Iron Metal Bed for Labor Dormitory 1 Pieces / (Min. Order)
- Brackets for Aluminum Gutter and Downpout 1 Pieces / (Min. Order)
- Antioxidant(Metal Deactivator) YM Metal Deactivator 1 Pieces / (Min. Order)
- Wood Grain PVC Membrane Foil for Ktichen Cabinet,Bedroom,Bathroom Decoration 1 Pieces / (Min. Order)
- 12V central ac fan motor with color wire 1 Pieces / (Min. Order)
- Mono-(6-(tetraethylenepentamine)-6-deoxy)-beta-Cyclodextrin 1 Pieces / (Min. Order)
- CuPb10SN10 Bimetallic Engine Bearing TSB-800 1 Pieces / (Min. Order)
- Metallurgical Mineral Dressing Used NPAM 1 Pieces / (Min. Order)
- Non-toxic calcium zinc complex heat stabilizer jcz-6503 from factory 1 Pieces / (Min. Order)
- Non-toxic calcium zinc complex heat stabilizer jcz-711 from factory 1 Pieces / (Min. Order)
- Non-toxic calcium zinc complex heat stabilizer jcz-6201 from factory 1 Pieces / (Min. Order)
- Non-toxic calcium zinc complex heat stabilizer jcz-6501 from factory 1 Pieces / (Min. Order)
- SA3-A850/125 Ride-on Full Automat 1 Pieces / (Min. Order)
- None Door Steel Office File Storage Cabinets Cupboards With Shelves 1 Pieces / (Min. Order)