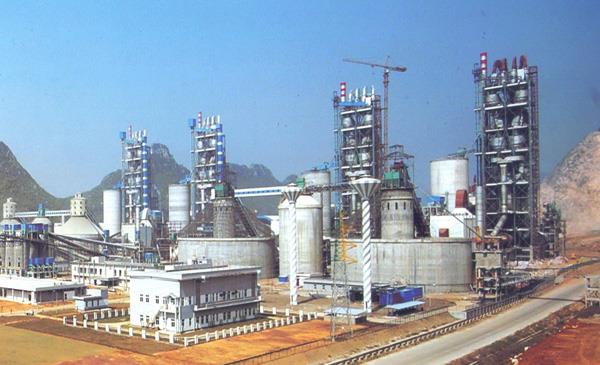
New Type Dry Process Cement
-
Min Order
1
-
Product Unit
Pieces
-
Origin
China Mainland
-
Payment
- Contact Now Start Order
- Favorites Share
- Description
Product Detail
2500 TPDDry Process Cement production line
Process Flow of 2500Tons/Day Dry Process Cement Plant:
The main process flow of this 2500t/d dry process cement plant is as follows:
1. Crushing, Conveying and Storing of Limestone.
First, limestone is crushed by the MB56/75 crusher. When the maximum feeding size is not more than 1500mm and the discharging size is not more than 75mm, the crushing capacity of this machine is 500 to 600t/h.
Second, the crushed limestone will be transported by belt conveyor to the F80m round prehomogenization yard whose storage capacity is 34100t.
Third, the crushed limestone will be prehomogenized and then stored in this yard. Additionally, the stacking capacity of our stacker is 800t/h, and the reclaiming capacity of reclaimer is 500t/h.
Finally, the prehomogenized limestone will be sent to the batching station for raw materials.
2. Storing, Crushing and Conveying of Auxiliary Raw Materials.
The open storage yard for sandstones has a specification of 60 m×20m, and a storage capacity of 5100t. And the open storage yard for iron ores has a specification of 32 m×20m, and a storage capacity of 2730 t.
PC1609 hammer crusher is used to crush both sandstones and iron ores. When the feeding size is not more than 600mm, and discharging size less than 25mm, its crushing capacity is 50 to 70t/h.
The crushed sandstones and iron ores will be sent by the belt conveyor to batching warehouse for storage.
The pulverized coal will be stored in the batching warehouse for storage through the self-discharging system.
3. Batching Station for Raw Materials.
In the batching station, there are four batching warehouses respectively for limestone, sandstones, iron ores, and pulverized coal, and their specifications are f12 m×25m, and storage capacity are 2200t,1600t, 2200t, and 770t respectively. Inside these warehouses, there are weighing feeders used to measure materials to be given.
4. Grinding of Raw Materials and Waste Gases Treating.
MLS3626 vertical mill is used to grind raw materials, and waste gases from preheater are applied in drying. The whole production capacity is 185t/h.
Grinded raw meal is separated by the fine powder separator, and then mixed with powder in the conditioning tower and electric environmental protection equipment. Finally it will be sent to the homogenizing warehouse for homogenization as well as storage.
Waste gases from the mill will take purification treatment in the electric environmental protection equipment before discharged into the air.
5. Homogenizing of Raw Meal.
Our CP homogenizing silo has a specification of F18m×50m, and its effective storage capacity is 9000t.
6. Calcining and Storing of Clinker.
The specification of our RF5/2500 decomposition furnace isF4.0×60m, and our round 2-f18×40m warehouse has an effective storage capacity of 2-10000t. Additionally, the final discharging gas has a dust content less than 100mg/m3 if in standard conditions.
7. Storing and Conveying of Raw Coal and Pulverized Coal.
Raw coal will be stored and prehomogenized in a crane room with a specification of 21m×113m and a storage capacity of 9300t. There are two raw coal silos in the crane room, and weighing feeder can also be found in that room. A MPF1713 coal grinder is used to grind coal. When the moisture of feeding materials is no more than 10%, the moisture of pulverized coal is no more than 1%, and the particle size of raw meal is no more than 50mm, the output of the whole system is 20t/h.
The pulverized coal will be sent to two silos for storage, and the purified waste gas is discharged into the atmosphere. There is also measuring system in these two silos.
8. Drying and Conveying of Slag and Crushing and Conveying of Gypsum.
The drying capacity of ourf2.4×18.350m dryer is more than 30t/h, and the open storage area has a storage capacity of 4000t. When the feeding size is no more than 600mm and the discharging size is no more than 25mm, the productivity of our PFC-1609 impact hammer crusher is 50 to 70t/h.
3000tpd new type dry process cement production line
Main process flow:
1. Limestone crushing: limestone from auto-dumper will enter into hopper, then it will be conveyed to limestone pre-homogenization yard by belt conveyor after crushing by hammer crusher. Then cantilever stacker will be used to stack & reclaim in layer. Stacked limestone will be transported to raw material proportioning station & limestone proportioning bin by belt conveyor. Set electromagnetic iron separator on inlet belt conveyor of bin to remove all possible iron parts in limestone. Set metal detector on head of belt conveyor to check whether there are iron parts in raw material to avoid damage to raw material roller press.
Raw material proportioning station configures limestone, silica, iron ore gauge and wet fly ash proportioning bin. At the bottom of each proportioning bin sets apron feeder and constant feeder, four raw materials will be discharged according to the requirements of proportioning by its constant feeder, mixed material will be fed into small bin of raw material roller press via belt conveyor.
2. Raw material grinding utilizes roller press together with ?4.6m×(10+3.5)m middle-discharge mill system, meanwhile high temperature waste gas exhausted from kiln tail will be used as hot source for drying. Material will be dried and classified by V type separator after extruded by roller press, while part of fine powder will be sent into raw meal homogenization silo via air side and bucket elevator after separating by high efficient separator. The other part of rough powder and wet fly ash will enter into raw mill for grinding. Material will be grinded and dried in raw mill, outlet raw mill will enter into separator via elevator, meanwhile rough powder will return back to mill and fine power will enter into raw meal homogenization silo via air slide and bucket elevator after separating. Outlet waste gas of mill via separator will be exhausted into the air after treated by EP filter of waste gas treating workshop.
3. Coal mill sets in kiln tail, part of waste gas of kiln tail will be used as hot source for drying raw coal after treated by cyclone. Waste gas of kiln tail will enter into EP filter at kiln tail directly after treated by air conditioning tower. The sprayed water volume of air conditioning tower can be auto-controlled according to the temperature of outlet waste gas, it makes the temperature of waste gas be in the allowable range of EP filter of kiln tail and the waste gas treated by dust collector will be exhausted into air by blower. The kiln ash collected by air conditioning tower will be sent into kiln feeding system or raw meal homogenization silo via conveying equipment. Configures one ?18m continuous raw meal homogenization silo, raw meal inside of silo will be discharged into mixing room from surrounding circle zone after being inflated in alternate partitions and the raw meal will be mixed evenly by inflated air. The inflated air at the bottom of silo will be supplied by relevant Roots blower. Homogenized raw meal will pass through air slide and bucket elevator after being measured and they will be fed to two inlets of double series pre-heater via distributor and air lock valve.
4. Burning workshop is composed of five-stage double series suspension pre-heater, calciner, rotary kiln, grate cooler and relevant dust collecting system with the capacity of 3000t clinker per day. Raw meal fed into pre-heater will be preheated by pre-heater and de-composed by calciner, and then it will be fed into kiln for sintering. Outlet clinker with high temperature will be cooled by grate cooler. Large block clinker will be crushed by crusher, and it will be sent into clinker silo via clinker chain type bucket elevator together with small clinker under air room. Part of the hot air from clinker bed will be used as 2nd air and 3rd air of kiln and calciner, the rest of waste gas will be exhausted into air after treated by EP filter. Clinker will sent to bulk car loading station via belt conveyor after being discharged via discharging device at bottom of silo and bulk clinker will be directly loaded into car by dustless bulk loader at the bottom of silo.
5. Coal powder manufacturing utilizes vertical grinding system and the high temperature waste gas exhausted from kiln tail will be used as hot source for drying. Raw coal will be fed into coal mill for drying and grinding via raw coal constant feeder, outlet coal powder will enter into bag type dust collector comply with air flow, qualified coal powder will be collected and sent into coal powder silo with load sensor via screw conveyor. Measured coal powder will be sent to kiln head burner and kiln tail calciner for sintering. Dust gas will be exhausted into air after being treated by static-free EP filer. Coal powder bin and bag type dust collector sets CO detector and explosion-proof valve.
The whole plant sets one central laboratory which will check all raw fuel, half-finished product and finished product; and one air compressor station which supply compressed air to the whole plant for production.
Energy-saving technical characteristics
The limestone crushing system, raw material grinding system, burning system, coal powder manufacturing system of this project utilizes one series self-developed, advanced, high efficient and energy saving system, technology and equipment.
1. Limestone crushing utilizes single-stage hammer crusher with imported technology, its process and process is very simple and the power consumption of unit product is low.
2. Raw material grinding utilizes roller press together with Æ4.6m×(10+3.5)m middle-discharge closed-circle mill system which can save about 5kW×h/t per unit raw meal compared with traditional middle discharge mill system and wind swept coal mill. It saves construction investment and reduces the power consumption of product.
3. Coal powder manufacturing utilizes energy-saving and high efficient vertical roller mill system which could save about 11.0kW×h/t power consumption of unit coal powder compared with traditional wind swept ball mill, dynamic rough powder separator and high concentration plenum pulse bag type dust collector system.
4. Clinker burning system utilizes NC type double series low pressure loss five –stage cyclone pre-heater and calciner system, NC high efficient rotary kiln, NC high efficient coal powder burner, control-flow type new technology cooler, etc. equipment with high performance which effectively reduces the heat consumption and power consumption of clinker burning. The heat consumption of clinker burning is less than 750×4.182kJ/kg.Cl and comprehensive clinker power consumption is less than 58kWh/t.Cl.
5. Material conveying utilizes high efficient, energy-saving process equipment with low consumption, so that the power consumption could be reduced to the maximum. Concerning bucket elevator will be used to convey raw meal into silo and pre-heater, it could save 2.5~3kW×h/t conveying power consumption of unit raw meal.
6. Utilizes DCS computer control system to monitor and control the whole production line which implements stable control, optimizing operation, energy-saving and consumption reduction and improve the labor capacity.
Comprehensive & effective utilization of heat energy, adequately utilizes the waste gas exhausted from kiln tail pre-heater as hot source for drying of raw grinding and raw coal drying of raw coal manufacturing system. Utilizes new technology cooler whose heat recovery could reach over 75%, it can not only recovers the heat energy of kiln clinker, but also improves the temperature of 2nd air and 3rd air and reduces the clinker burning heat consumption.
8. Kiln burning device utilizes multi-pipes coal burner which could reduce the 1st air rate of kiln to about 10%, improve high temperature 2nd air volume, improve the burning condition inside of kiln and raise the burning efficiency.
During the engineering design, we try our best to implement better process flow, avoid round-trip transportation of material and save material conveying power consumption. Strengthen measuring, improve efficiency, reduce raw material consumption and product loss, sets various measuring equipment and instruments with high quality and high accuracy in every important point and sets various dust collecting equipment with stable operation and high efficiency in every dust-raising point which makes the bug dust exhaustion meet the standard, this could prevent circle environment and reduce pollution.
Equipments of 5000tpd new type dry process cement production line
Main processing flow sheet
Using single hammer crusher for limestone crushing, the processe is vry simple and the eletrical composution is lower. Adopt vertical system for raw meal grinding, compare with tranditional middle discharging system and air swept system; it can save 5-7kW×h/t per unit raw material.
5 stage preheater was designed of low loss technology. The main structure feature is big spiral casing, short cylinder, in the meantime, there is guide plate and rectifier etc. So the system resistance reduce a lot. Compare with traditional preheater, the electrical consumption can be reduced to 15%-20%.
Clinker cooler is grate cooler with latest technology. The required air volume for cooling and waste gas is 0.6-0.8Nm3/kg-cl compared with second generation grate cooler. Therefore the electrical consumption for cooling air fan and waste gas exhaust fan can be reduced more than 20%.
For coal powder preparation, we using vertical mill. Compare with traditional produce flow sheet with air swept mill + dynamic separator + high concentration air tank pulse bag filter, it can save about 11.0kW×h/t per unit coal powder.
Except coal powder feeding to kiln and furnace, all the materials inside plant are transported by process equipments with high efficiency, energy saving, low consumption, in order to save electrical consumption as more as we can. In terms of bucket elevator for raw meal transportation to silo and preheater, it can save 2.5-3kW×h/t per unit.
Considering electrical saving, smooth and tight process flow sheet, reduce production chain, try to avoid material transportation in circle, shorten the transport distance and height, then the transport consumption can be reduced. Enforcing measuring, increasing efficiency, reducer consumption for raw fuel and product. Using various measuring equipments and tools with high quality and precision in all the important sections. Install various duct collecting equipments at all dust point to control the content, which can not only protect the environment, reduce pollution, but can reduce production loss for raw fuel and product. In the meantime, energy and production cost are reduced accordingly.
Belt bucket elevator is used for kiln inlet feeding. Air inlet is about 70000m3/h less than traditional air lift pump, it can increase the heat efficiency for preheater. Adopt circulating water system for equipment cooling water, the use ratio can be reach to 95%, saving water consumption. And we also make efforts to reduce heating loss on surface of equipment and tube. Choosing energy saving equipments, such as motor, fan etc. For fan and pump, VVVF electrical contract equipments are used. And we also choose energy saving equipments with high efficiency but low loss, such as transformer, contactor, lamps etc.
Main equipments
Department | Equipment name | Type, spec. & performance |
Limestone crushing | Hammer crusher | TKLPC20.22A feeding size<1100mm,discharging size<75mm ;capacity: 700t/h |
Siltstone crushing | Jaw crusher | PE-900X1200 feeding size<750mm,discharging size<150mm;capacity: 200t/h |
Cone crusher | PYS-1215 feeding size <150mm,discharging size<30mm ;capacity: 200t/h | |
Limestone prehomogenization yard | Cantilever stacker | Stack capacity: 1400t/h |
Reclaimering capacity: 500t/h | ||
Siltstone prehomogenization yard | Mobile stacker | Stack capcity: 200t/h |
Chain plate-type reclaimer | Reclaimering capacity: 110--130t/h | |
Raw coal prehomogenization yard | Travelling stacker | Stack capcity: 200t/h |
Bridge type scraper reclaimer | Reclaimering capacity:: 100t/h | |
Raw meal grinding and waste gas treatment | Vertical mill | MLS4531,capacity360--400t/h;feeding moisture<6%,output moisture<0.5%;feeding size<100mm,output sizeR80µm<12% |
Raw meal mill fan | Air volume:860000m3/h,full pressure:9500Pa | |
Kiln inlet high temperature fan | Air volume:860000m3/h,full pressure:7500Pa | |
High concentration electrostatic precipitator | BS930,electric field sectional area:~310 m2;air volume:820000m3/h;outlet dust content(standard)=50mg/m3 | |
Coal powder preparation | Vertical mill | MPF2116,capacity:38~45t/h;feeding moisture <12%,output moisture <1%;feeding size:<25mm, output size:R80µm<12% |
Firing system | Rotary kiln | F4.8×74m,inclination:4%,support no.:3;speed:0.6~4.0r/min,installed power:630kW;capacity: 5000t/d |
Preheater and calciner | Five stage double series preheater + calciner | |
Control flow grate cooler | LBT36352,grate bed area: 119.6 m2 ;feeding temperature:1400?,discharging temperature :65?+ ambient temperature | |
Kiln outlet electrostatic precipitator | Air flow:550000m3/h, electric field sectional area:196m2;inlet dust content: =30 g/m3;outlet dust content:=50mg/Nm3 |
Pengfei Group is one of the professional new type dry process cement manufacturers and suppliers in China. Our factory can offer you low price but quality, newest and advanced products made in China. We are one of the most famous such brands. Welcome to buy our customized, durable and easy-maintainable new type dry process cement and also welcome to check the quotation with us.
- Flexible Protection Network 1 Pieces / (Min. Order)
- Sheet Metal Processing 1 Pieces / (Min. Order)
- Stamping Processing 1 Pieces / (Min. Order)
- Tenth-Custom Processing 1 Pieces / (Min. Order)
- Metal Shell Processing 1 Pieces / (Min. Order)
- Metal Case Processing 1 Pieces / (Min. Order)
- Tantalum Ground Ring 1 Pieces / (Min. Order)
- Ductile Iron Grating 1 Pieces / (Min. Order)
- The Invisible Socks Knitting 1 Pieces / (Min. Order)
- 1.56 White Progressive RX Lens 1 Pieces / (Min. Order)
- Retractable Dome Awning 1 Pieces / (Min. Order)
- Sheet Metal Processing 1 Pieces / (Min. Order)
- Cute Pigeon Brooch Pin 1 Pieces / (Min. Order)
- Customized EPC Casting 1 Pieces / (Min. Order)
-
Conductive Yarn/Textile/Fabric/Garment
US $5.39-15.04 / Price
1 Pieces / (Min. Order) -
Anti-bacterial Yarn/Socks/Underwear/Sports Wear
US $7.86-17.73 / Price
1 Pieces / (Min. Order) -
Conductive Textile Shielding Fabric for Women/Amy
US $9.9-18.68 / Price
1 Pieces / (Min. Order) -
Conductive X-static Fabric/yarn/Tetile
US $8.94-11.57 / Price
1 Pieces / (Min. Order) -
Silver Ion Modified Self Clean Fabric Polyester Yarn
US $6.8-18.49 / Price
1 Pieces / (Min. Order)